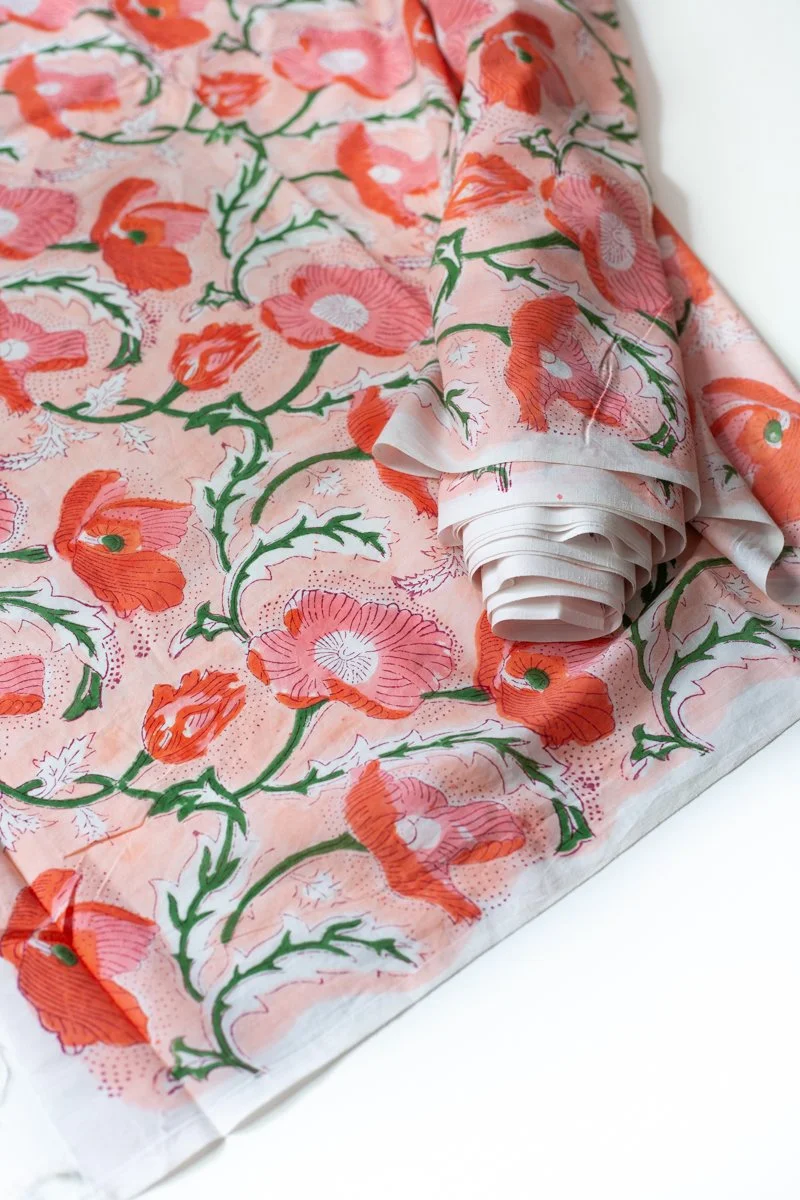
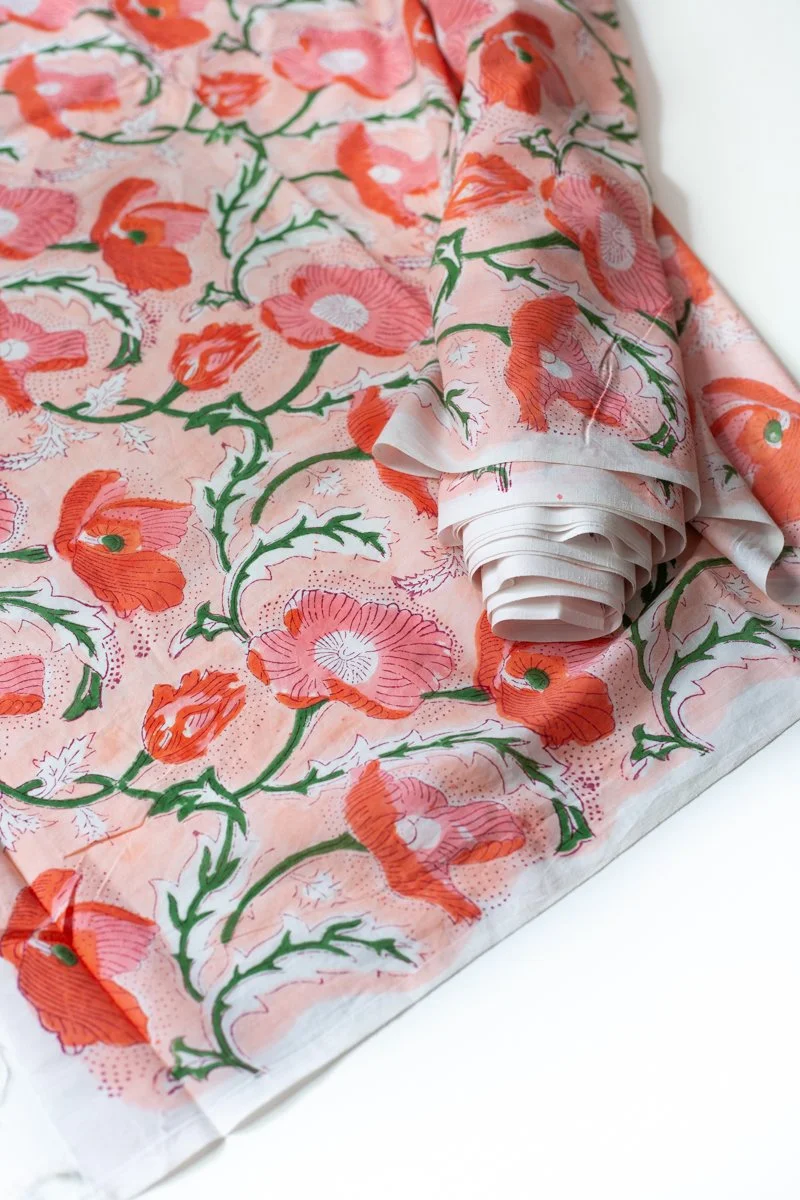
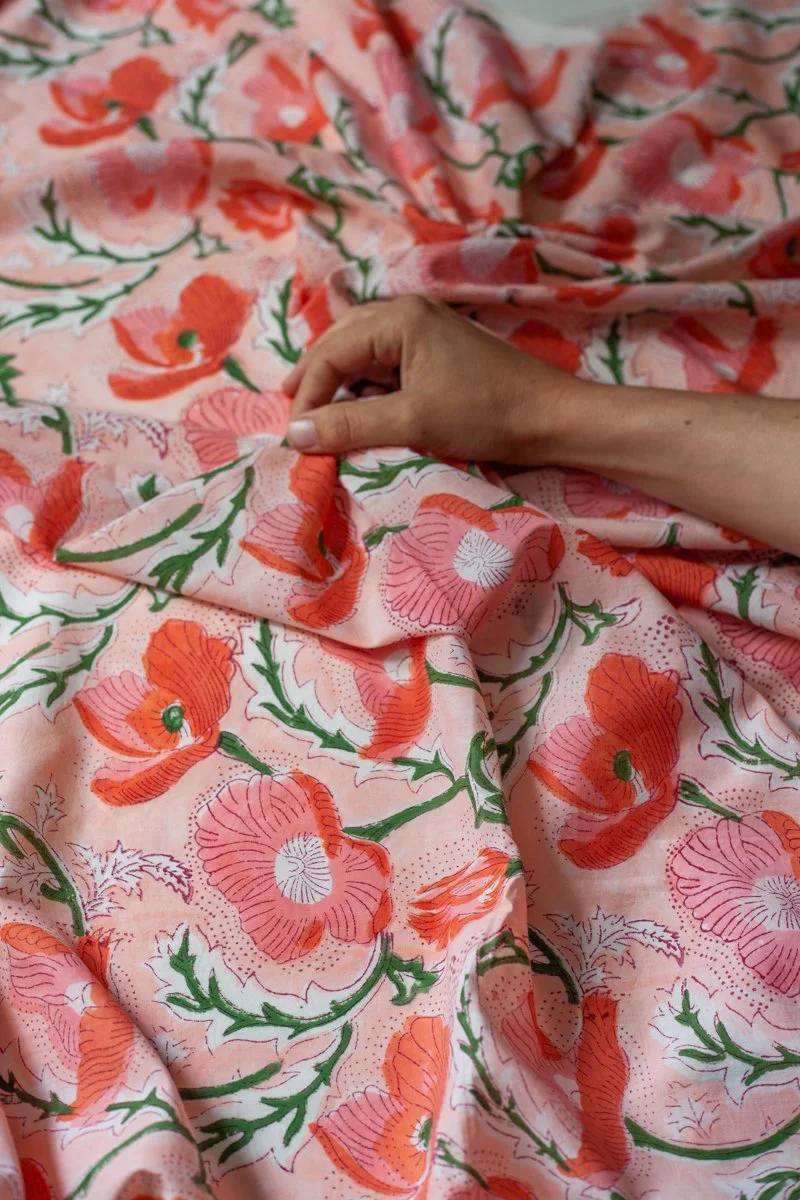
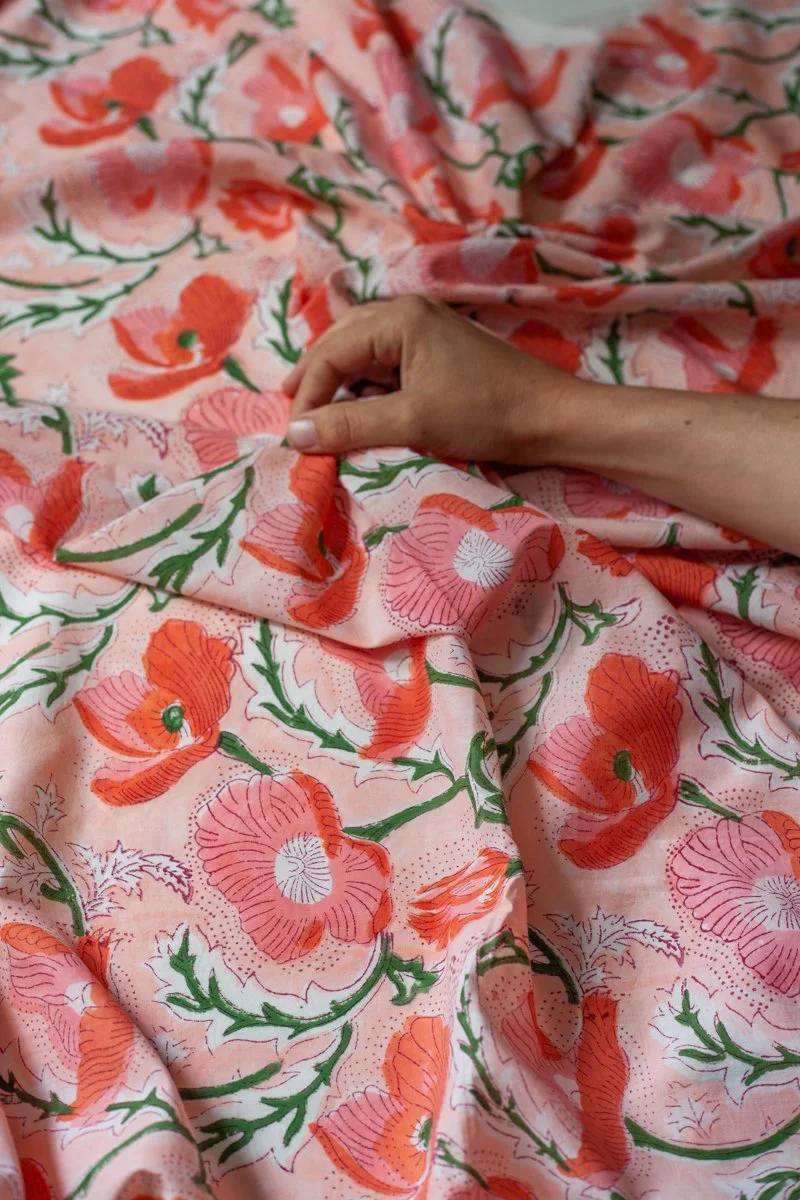
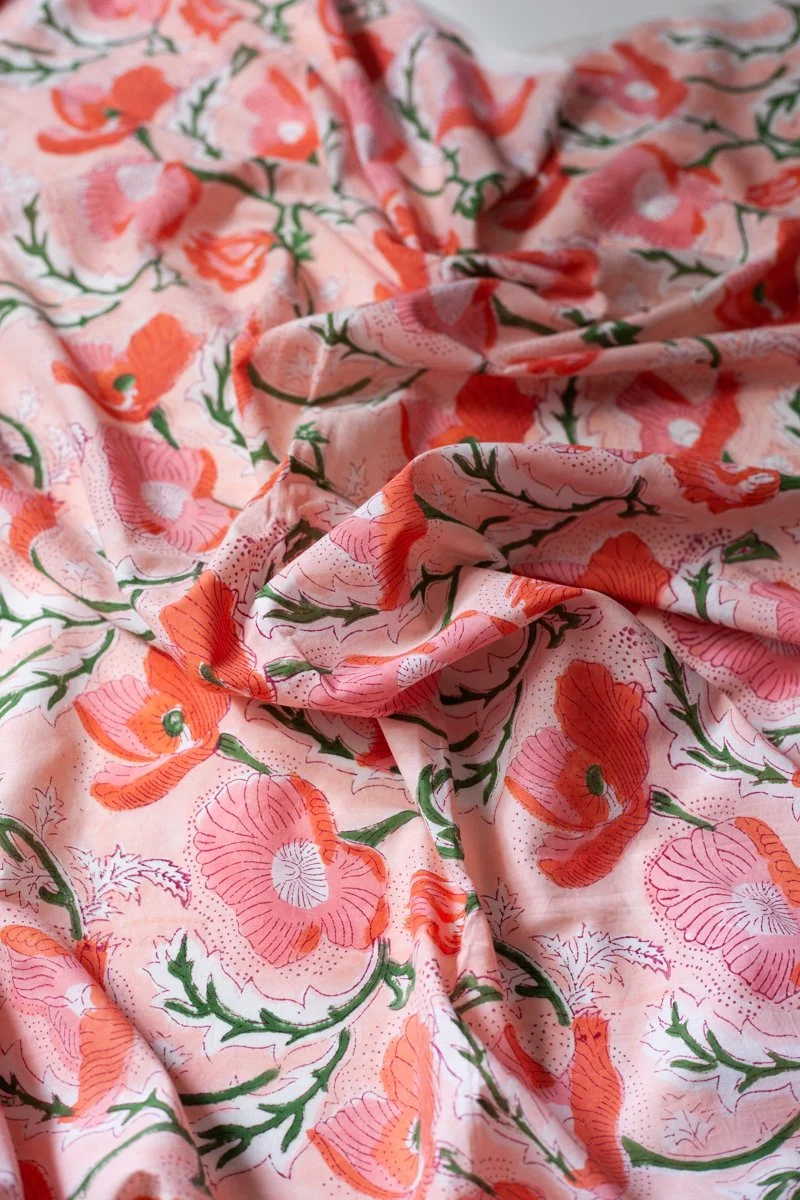
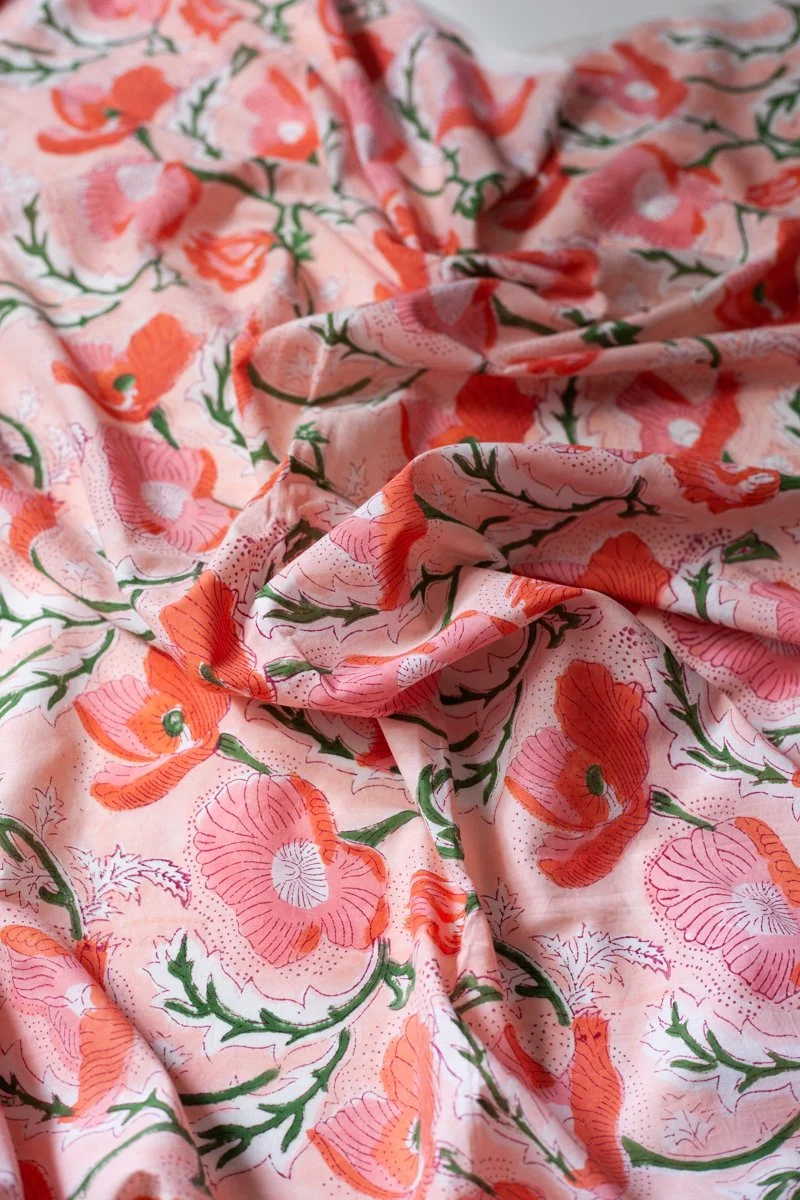
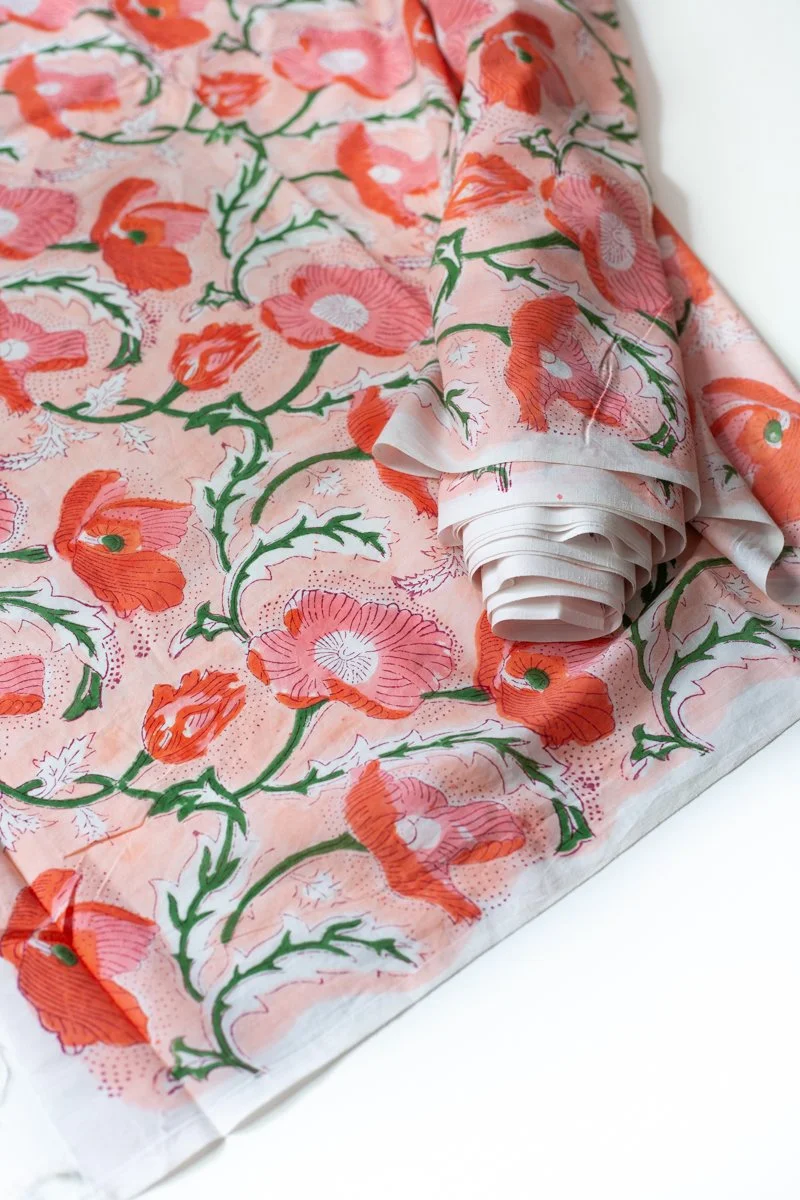
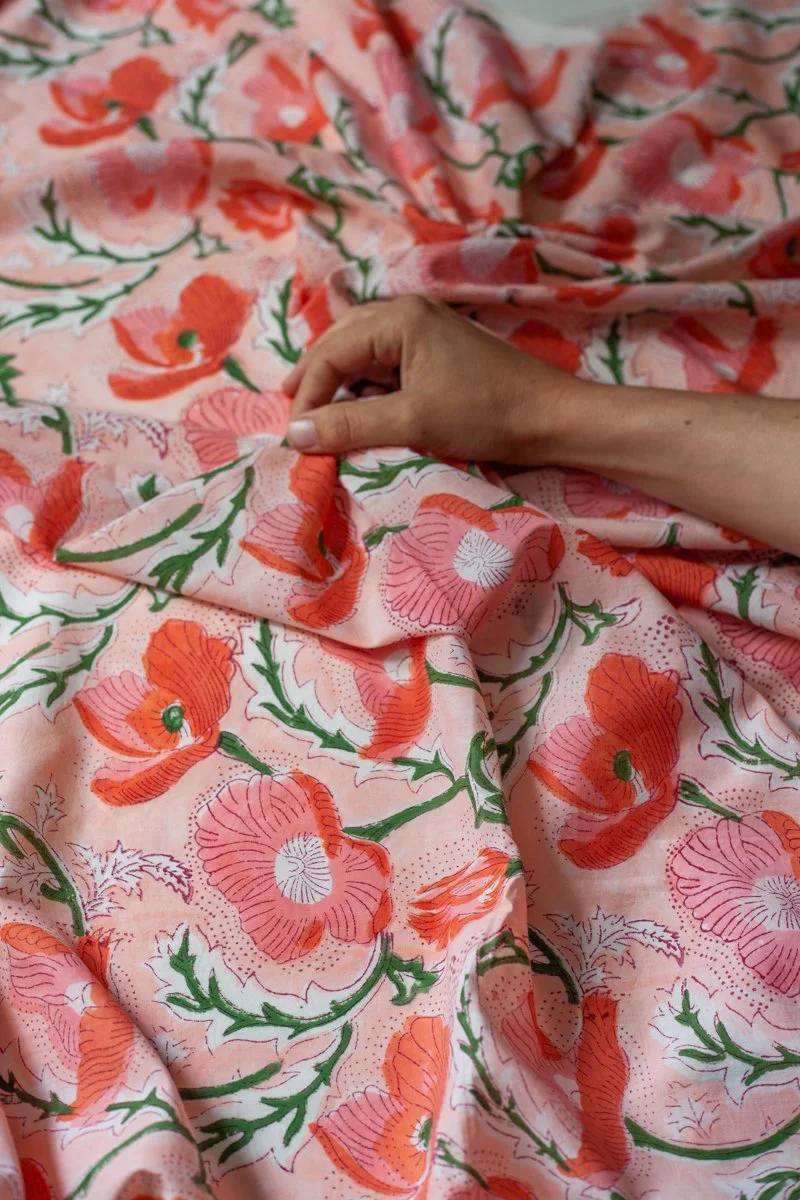
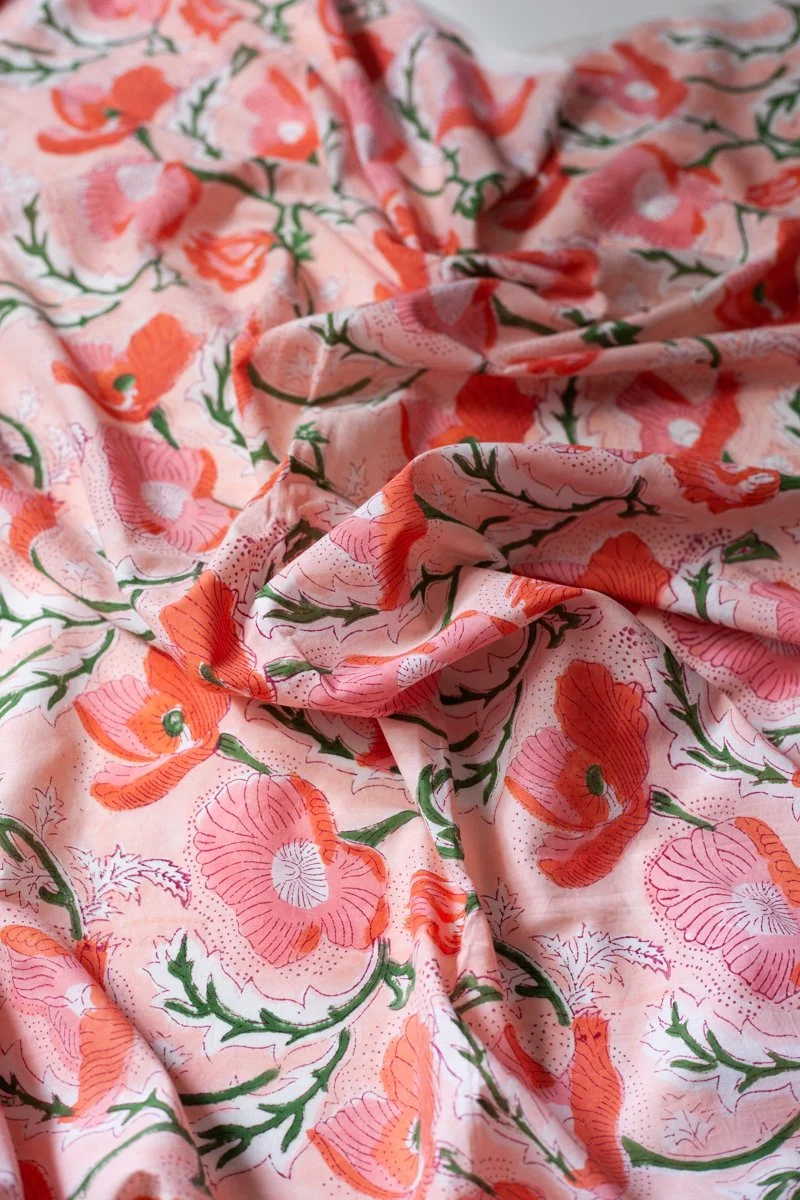
Block Printed Indian Cotton, vegetable + clay dyed- Madder Poppies
Light weight: suitable for shirting, dressmaking etc & some home applications.
Block printed cotton is an ancient Indian textile tradition, and the cloth offered here is made utilizing the same natural dyes and processes (using hand-carved wooden blocks for stamping) that have been practiced since the beginning. Additional info on the process is continued below.
All of our cotton block prints are sourced ourselves. We love the soft hand-loomed cotton and the imperfections that come from hand printing.
approx 44”wide and sold by the yard.
wash on cold/delicate cycle with mild detergent, adding one spoonful of white vinegar per yard of fabric to help fix the natural dye. Do not tumble dry.
Purchase a sample to check the color and weight
100% cotton, made in Rajasthan, India
Light weight: suitable for shirting, dressmaking etc & some home applications.
Block printed cotton is an ancient Indian textile tradition, and the cloth offered here is made utilizing the same natural dyes and processes (using hand-carved wooden blocks for stamping) that have been practiced since the beginning. Additional info on the process is continued below.
All of our cotton block prints are sourced ourselves. We love the soft hand-loomed cotton and the imperfections that come from hand printing.
approx 44”wide and sold by the yard.
wash on cold/delicate cycle with mild detergent, adding one spoonful of white vinegar per yard of fabric to help fix the natural dye. Do not tumble dry.
Purchase a sample to check the color and weight
100% cotton, made in Rajasthan, India
Light weight: suitable for shirting, dressmaking etc & some home applications.
Block printed cotton is an ancient Indian textile tradition, and the cloth offered here is made utilizing the same natural dyes and processes (using hand-carved wooden blocks for stamping) that have been practiced since the beginning. Additional info on the process is continued below.
All of our cotton block prints are sourced ourselves. We love the soft hand-loomed cotton and the imperfections that come from hand printing.
approx 44”wide and sold by the yard.
wash on cold/delicate cycle with mild detergent, adding one spoonful of white vinegar per yard of fabric to help fix the natural dye. Do not tumble dry.
Purchase a sample to check the color and weight
100% cotton, made in Rajasthan, India
The recorded history of Indian block printed fabrics dates back to the Indus Valley civilisation, around 3500 to 1300 BC. From the Harappan period onwards, the export of textiles, especially cotton, is confirmed. During the Mohenjo-daro site excavation, needles, spindles, and cotton fibres dyed with Madder (a red dye or pigment obtained from the root of the madder plant) were excavated. This proves that Harappan artists were familiar with Mordants (dye fixatives)
Today, the art form is practiced in the states of Andhra Pradesh, West Bengal, Punjab, Madhya Pradesh, Uttar Pradesh, Maharashtra, Rajasthan (where our cloth is from) and Gujarat.
The process of block printing is a tedious one—the blocks themselves require 10-15 days to be perfected. It all begins with a fabric that is first washed free of starch. If tie-dyeing is needed, it is done at this stage, and if the fabric is already dyed, it is washed to remove excess color, post which it is dried in the sun. The next step sees the fabric pinned on the printing table. Meanwhile, the colors are prepared and kept on a tray containing glue and pigment binder to ensure a soft base for the color, and to allow it to easily spread on the block.
These blocks are made using woods such as teak, sycamore and pear, and are lovingly hand-carved in a myriad of intricate designs that are first made using chalk paste or a pencil on paper. Post this, they are soaked in oil for 10-15 days to soften the timber.
Once the blocks are ready, they are dipped in the colour and then pressed on to the fabric. This process is repeated over and over again until the length of the fabric is complete. Precision is demanded by the artisans to ensure there are no breaks in the motifs. If there are multiple colours, other blocks are used and the artisan waits for the first print to dry first.
The fabrics are left to dry in the sun, and then rolled in a newspaper to prevent them from sticking to each other. The post-printing process sees them being steamed, washed in water, dried in the sun again, and lastly, being ironed.
There are only three widely-used techniques of block printing in India—direct printing, resist printing and discharge printing. Direct printing sees the fabric bleached first, then dyed and finally printed using carved blocks (first the outline blocks, and then to blocks to fill in colour). Resist printing requires some areas of the fabric to be protected from the dye, which are shielded with the use of clay and resin. The dyed fabric is then washed, but the dye spreads through the protected areas, causing a rippled effect. Next, further use of blocks add desired designs. The last technique of discharge printing, on the other hand, sees the use of chemicals to remove portions from dyed fabric which are then filled in with different colours.